Powder-Coated Process: Gate Fittings & Hinges
Powder coating has revolutionized the way gate hardware and hinges are finished, offering unmatched durability and aesthetic appeal. This process involves applying a heat-cured, electrostatically charged coating that forms a tough, protective layer, shielding hardware from rust, chipping, and fading - essential for outdoor fittings exposed to the elements. In addition to its practical benefits, powder coating provides endless design options with various colors and finishes to complement any gate or outdoor space. For heavy-duty hardware like D&D Technologies' SHUT IT hinges, powder coating enhances their resilience and longevity and ensures they maintain their sleek, high-performance appearance for years to come.
The Powder-Coating Process
Powder coating is a dry finishing process widely used to enhance the durability and appearance of metal components, such as gate hardware and hinges. The process begins with fine particles of pigment and resin that are electrostatically charged and sprayed onto the surface of the metal. This electrostatic charge ensures that the powder adheres evenly to the metal surface, covering every detail precisely. Unlike liquid paints, powder coating does not require solvents, making it an environmentally friendly option with minimal waste.
The coated item is curing Once the powder is applied. This involves placing the hardware in an industrial oven exposed to high temperatures, typically around 400°F (204°C). The heat causes the powder particles to melt and fuse, forming a smooth, uniform, tough, and aesthetically pleasing layer. The result is a durable finish that resists corrosion, chipping, and fading, making it ideal for outdoor gate hardware exposed to the elements.
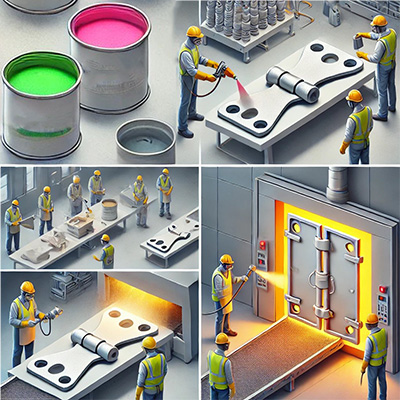
Manufacturer Powder-Coating Process
Surface Preparation:
- Use industrial sandblasting equipment to remove dirt, rust, and previous coatings, ensuring a clean, textured surface.
- Employ high-grade degreasers or chemical treatments to eliminate oils and contaminants.
Powder Application:
- Utilize advanced electrostatic spray systems in a controlled booth to apply the powder coating evenly.
- Ensure consistent electrostatic charge and optimal environmental conditions to achieve a uniform finish.
Curing:
- Transfer the coated hardware to an industrial curing oven preheated to the precise temperature specified by the powder manufacturer.
- To ensure proper bonding, Maintain strict time and temperature control, typically at 400°F (204°C) for 10-20 minutes.
Cooling and Quality Control:
- Allow the hardware to cool in a designated cooling area to prevent contamination.
- Inspect each piece using quality control standards to ensure the coating is smooth, uniform, and defects-free.
What Materials Can Be Powder-Coated?
- Steel: A common choice for gate hardware, steel is an excellent candidate for powder coating due to its ability to withstand high temperatures and its strength, making it ideal for hinges, brackets, and frames.
- Aluminum: Lightweight and corrosion-resistant, aluminum hardware like latches and decorative fittings can also be powder-coated for added protection and a sleek finish.
- Iron: Wrought iron components, including hinges and decorative elements, benefit significantly from powder coating, as it enhances their resistance to rust and other outdoor elements.
What Cannot Be Powder-Coated?
Heat-sensitive materials, such as thin metals, plastic inserts, rubber seals, or other non-metal components, cannot withstand the high temperatures required for powder coating and may warp, melt, or degrade during the curing process. Components like internal bushings, gaskets, or bearings often need to be removed before coating and reassembled afterward, which can be time-consuming and challenging. For a more efficient solution, manufacturers like D&D Technologies offer specialized pre-powder-coated hardware, such as SHUT IT hinges with high-temperature sealed bearings, designed to handle the powder coating process without disassembly, ensuring durability, performance, and a flawless finish.
What Kinds of Hinges Can and Cannot Be Powder-Coated?
Not all D&D Technologies gate hinges suit powder coating. While some are designed to handle the process, others may be compromised due to their materials or construction. Knowing which hinges are compatible ensures durability and performance. Here is a list of D&D Technology hinge series with more information:
Can Be Powder Coated
- Shut It BadAss Hinges: Yes, most Shut It BadAss hinges are designed to be powder-coated, especially those with high-temperature sealed bearings (e.g., Face Mount Weld-On, VersaWeld, and Powder Coated Face Mount Bolt-On models).
- Stainless Steel Hinges: Yes, stainless steel hinges can be powder-coated, and some models are available pre-powder-coated from the manufacturer.
Cannot Be Powder Coated
- TruClose Hinges: No, these hinges are not designed to be powder-coated. Powder coating could interfere with their self-closing mechanism and polymer construction.
- KwikFit Hinges: No, these hinges are not designed to be powder-coated due to their plastic/nylon components, which are not compatible with the high heat involved in powder coating.
- SureClose Hinges: No, these hinges are typically not intended for powder coating. They are engineered with precision components that might be affected by the coating process.
- WoodHardware Hinges: No, these are generally not powder-coating friendly, as they often feature components that cannot withstand the heat or are pre-finished.
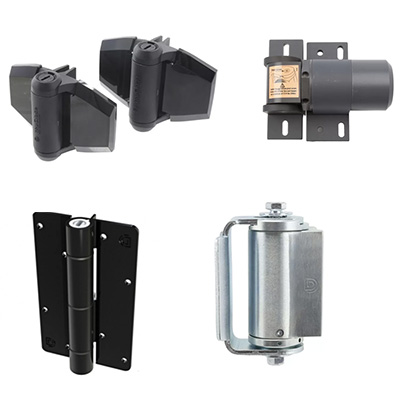
Now that you know which hinges can be safely powder-coated, you might wonder how to tackle the process yourself. DIY powder-coating is a practical and rewarding way to enhance the durability and appearance of your hardware. With the right preparation, equipment, and techniques, you can achieve a professional-grade finish at home while ensuring the hinges maintain functionality and performance.
Reality of DIY Powder-Coating
While the basic steps of powder coating are similar, the processes used by manufacturers and DIY enthusiasts vary significantly in scale, equipment, and precision. Manufacturers rely on industrial-grade tools like high-powered sandblasters, advanced electrostatic spray systems, and large curing ovens to ensure consistent, high-quality finishes with precise temperature control and superior durability. These professional setups are ideal for handling large quantities or intricate components, delivering results that meet rigorous standards.
In contrast, DIY powder coating typically uses smaller, more affordable equipment like portable sandblasters and home-use powder coating guns, often paired with household ovens for curing. While this approach offers accessibility and flexibility for small projects or touch-ups, it can lead to uneven heating and less durable results. DIY methods are best suited for small-scale items like gate hinges or accessories, but for larger or critical components, such as heavy-duty hinges, professional powder coating remains the more reliable choice for ensuring durability and a flawless finish.
What Makes DIY Powder Coating Feasible:
- Accessible Equipment: Affordable powder coating kits, such as electrostatic spray guns, are available for home use. Combined with a dedicated oven (not used for food), these make it possible to do small jobs at home.
- Smaller Projects: DIY powder coating works well for single items like a hinge or bracket, where precision and quality control are easier to manage.
- Preparation Methods: Basic tools like wire brushes, sandpaper, or small sandblasters can help achieve a clean surface for coating.
Challenges of DIY Powder Coating:
- Curing Limitations: A household oven may not heat hardware evenly or maintain the precise temperature needed for consistent results. This can lead to an uneven finish or reduced durability.
- Quality of Equipment: DIY kits may lack the power and precision of industrial equipment, resulting in less uniform powder application.
- Environmental Factors: Professional setups include controlled environments to prevent contamination and ensure even coating. In a home setup, dust, humidity, or airflow can interfere with the process.
- Material Suitability: Not all hardware is suitable for DIY powder coating, especially items with complex shapes, non-metal components, or sensitive parts.
- Durable, long-lasting finish that resists chipping, scratching, and fading.
- Superior protection against rust, corrosion, and weather damage.
- Eco-friendly process with minimal waste and no harmful solvents.
- Provides a smooth, uniform appearance with customizable colors and textures.
- Ideal for outdoor applications and high-traffic areas requiring low maintenance.
Benefits of Powder-Coated Fittings & Hardware
Powder-coated fittings and hardware provide a range of advantages that make them an excellent choice for both functional and aesthetic purposes. The process creates a tough, long-lasting finish that resists chipping, scratching, and fading, ensuring durability even in harsh conditions. Powder coating protects against rust and corrosion, making it ideal for outdoor applications. Beyond its practical benefits, powder coating offers a clean, uniform appearance with various color and texture options, allowing for customization. Additionally, it is an eco-friendly option, as it produces minimal waste and avoids the use of harmful solvents.
Powder coating offers numerous advantages for gate hinges and hardware, providing a durable, corrosion-resistant finish that enhances functionality and appearance. The sleek, uniform coating ensures long-lasting performance, especially for outdoor applications, while reducing maintenance needs. For those looking for quality options, GateHardwareCenter offers a wide selection of powder-coated gate fittings and hardware, including hinges specifically designed to withstand the rigors of the powder-coating process. Their products combine durability with aesthetic appeal, making them reliable for any project.
Before starting a powder-coating project, ensuring the materials and components are suitable for the process is important. Some hardware may not be compatible with others due to their construction or material properties. If you're uncertain, consulting a professional can help you make informed decisions and achieve the best results. For convenience and quality, consider exploring our pre-powder-coated options, including ready-to-use gate hardware that saves time and effort while ensuring excellent performance.
If you have further questions about gate fittings and hardware, including powder-coated options, please contact our sales representatives. They are happy to help in any way they can!
Contact Us